Supply chain for equipment and materials affected by constraints on ocean and inland transportation
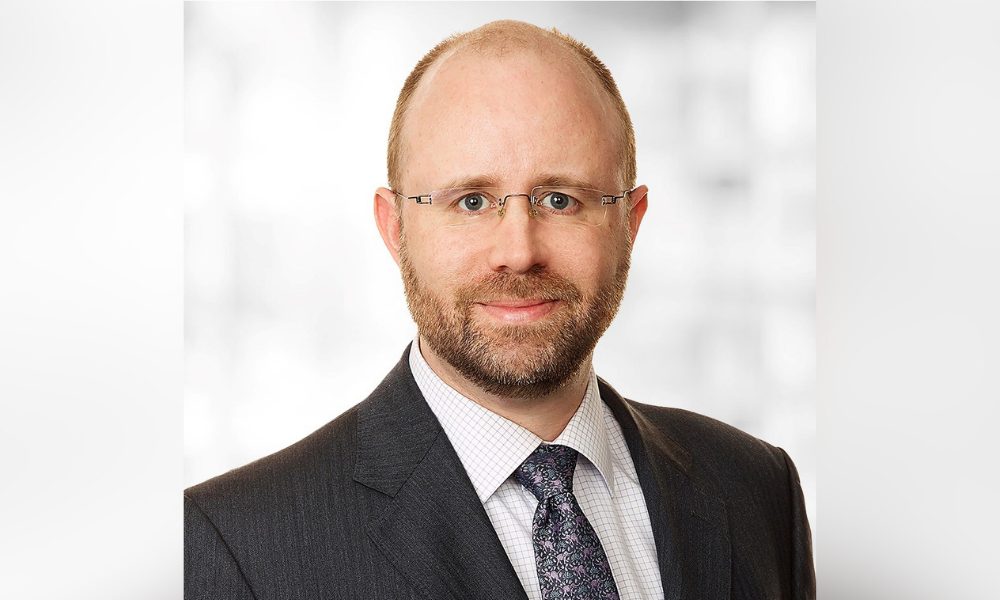
A year and a half in, changes to Ontario’s Construction Act that introduced prompt payment and adjudication have evidently not resulted in a remarkable uptick in payment disputes or requests for adjudication in the construction industry. What has made a difference, though, are supply chain issues brought about by the COVID-19 pandemic.
Driving some of the construction industry disputes is not only COVID’s continuing impact on managing a healthy workforce, but “the impact on the supply chain, and particularly for equipment and materials that are being manufactured overseas, and the constraints on ocean and even inland transportation,” says Mark Johnson.
Pent-up consumer demand that began last year – including for home renovations – as well as new infrastructure projects is having a big impact on projects that need to get their supplies from Asia to North America, and the cost and schedule for that is becoming highly unpredictable, says Johnson, a partner in Blake, Cassels & Graydon LLP’s Ottawa and Toronto offices who specializes in major power, infrastructure and public-private partnership (P3) projects.
The supply chain for equipment and materials manufactured overseas have been particularly affected due to constraints placed on ocean and even inland transportation, notes Johnson, who will be a panellist for Canadian Lawyer’s Construction Law webinar on Sept. 22.
“That creates real problems both for bidding projects -- the uncertainty of knowing whether or not this current environment will continue into next year or the year after -- and for existing projects that were priced before all the transportation issues hit,” he says, and also emphasizes “the need for fast, efficient dispute resolution.”
Since part of government stimulus during the pandemic has been new infrastructure projects on both sides of the Canada-U.S. border, “you’re competing for resources, transportation and shipping in a way that wasn't the case six months ago or a year ago.”
Short-cycle fluctuations in commodity prices also makes it very difficult for there to be price certainty, he adds.
For example, lumber prices reached market highs over the past year, but have fallen precipitously since May, as warmer weather and the easing of COVID-19 restrictions across the country have resulted in Canadians travelling more and doing home renos less. Canadian steel prices were up 51 per cent year over year in July, the biggest year-over-year increase on record, though are expected to remain strong.
“Commodity prices always fluctuate, but the spikes are hard to deal with when the demand is being driven by factors that aren’t the usual factors,” says Johnson, such as home renos and new home starts “to a much greater degree than ever.” Whether that surge has now cleared, “it’s hard to say.”
And whether supply chain issues will be resolved in the next year, “maybe, but nobody's going to be willing to bet their company on it,” he adds.
“The strain for project owners procuring projects and constructors bidding projects right now comes from the challenge of bidding certain elements of construction on a fixed price basis when there is considerable volatility in the supply chain for those elements.”
Neither project owners nor contractors have much control over the current global supply chain interruptions/shortages or commodity price volatilities. On the one hand, contractors run the risk of significantly under-pricing a supply risk that they can’t control or mitigate (both as to time and cost), but on the other hand, project owners risk significantly overpaying for a supply risk that may never materialize, he says.
“Other than delaying projects entirely, there are a few ways to mitigate the risk,” Johnson notes. “One is to restructure projects to either remove problematic elements, or, to diminish the timing risk they present.”